Nuevo concepto para materiales y producción reduce drásticamente el tiempo de fabricación para las puertas de los aviones
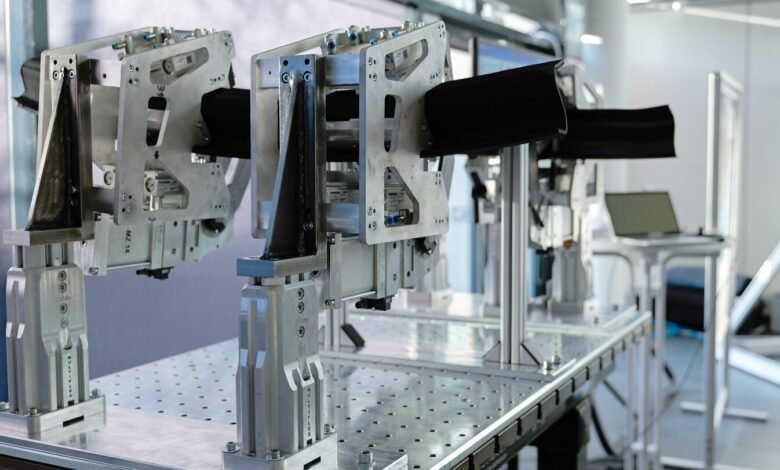
Elemento de sujeción desarrollado en Fraunhofer IWU para sujeción automatizada y unión de compuestos de fibra de carbono termoplástico en puertas de aeronaves (por ejemplo, haz cross). Crédito: Fraunhofer iwu
Las puertas de los aviones de pasajeros todavía se fabrican principalmente a mano. Un aspecto particularmente lento es ensamblar las estructuras de la puerta con tornillos y remaches. Se requieren numerosos pasos intermedios para evitar el contacto directo entre diferentes materiales, lo que de otro modo conduciría a la corrosión.
Sin embargo, reemplazar el aluminio, el titanio y las termosets con compuestos principalmente de fibra de carbono termoplástica (CFRP), que se pueden soldar automáticamente sin separar las capas, hace que el proceso sea mucho más rápido. El tiempo de fabricación para la estructura de la puerta cae de 110 horas a 4. El proyecto Tavieda de Fraunhofer Iwu, Fraunhofer LBF, Trelleborg y Airbus Helicopters lo han demostrado claramente.
Otro factor clave para acortar los tiempos de ensamblaje es el diseño modular para diferentes variantes de la puerta de la aeronave. El equipo del proyecto buscó específicamente componentes en varios modelos de puertas que pudieran estandarizarse, y encontró éxito, por ejemplo, con el rayo transversal. Los investigadores diseñaron una línea de ensamblaje totalmente automatizada para los modelos más comunes y accesorios desarrollados y elementos de sujeción adecuados para la resistencia y las tecnologías de soldadura ultrasónica.
Procesos de ensamblaje/unión totalmente automatizados y logística para la estructura de la puerta. Crédito: Fraunhofer iwu
Desde la artesanía del taller hasta la fabricación industrial de alto rango
El Dr. Rayk Fritzsche, plomo del proyecto en Fraunhofer Iwu, declaró: “Junto con nuestros colegas en Airbus, analizamos de cerca todas las estructuras de las puertas para adaptar las geometrías para la sujeción y la unión automática. Como resultado, podríamos reorganizar y automatizar completamente los pasos individuales. Esto, esta manera, redujo el momento de liderazgo a una fracción de lo que solía ser,” “.” “.” “.” “.” “.” El trabajo manual ahora solo se requiere para instalar el mecanismo de bloqueo.
Dos líneas de ensamblaje y unión casi idénticas aseguran la redundancia si una línea no está disponible. Gracias a las medidas de estandarización, ahora se pueden organizar lotes de 10 puertas, lo que permite una reorganización de línea completamente automatizada al final de cada turno para acomodar la siguiente serie de modelos. Con una capacidad de producción de 4.000 puertas por año, el nuevo material y concepto de producción conduce a importantes beneficios de escalabilidad.
Como parte de un nuevo enfoque, el modelado de costos se integró directamente en el entorno de simulación, lo que permite el cálculo simultáneo de los costos unitarios junto con los resultados de la simulación. Crédito: Fraunhofer Iwu Fraunhofer LBF desarrolló y validó la tecnología de medición experimental para sellos de puertas de aeronaves integrados en el sensor en el proyecto Tavieda; El socio del proyecto Trelleborg desarrolló la nueva geometría de sellado con, por ejemplo, la ayuda de simulaciones de elementos finitos. En este proceso, el componente bajo consideración se divide prácticamente en un número limitado de elementos geométricos simples y pequeños (elementos finitos). Crédito: Fraunhofer iwu
¿Invertir en nuevos equipos de producción vale la pena al final?
Maxi Grobis, del equipo de planificación, simulación y evaluación de fábrica de IWU, simuló todos los aspectos técnicos y económicos de la nueva línea de ensamblaje, factores que a menudo se influyen entre sí. Los criterios clave de evaluación técnica incluyeron complejidad de productos y procesos, oportunidades y riesgos de automatización (especialmente en relación con la flexibilidad y la adaptabilidad), y la disponibilidad general del sistema en una cadena de sistemas automatizados individuales.
Automatizar solo por el bien de la automatización no era una opción. Grobis enfatizó: “Para ofrecer una solución verdaderamente integrada, analizamos todo el proceso de producción y ensamblaje de la puerta y lo traducimos en un modelo de costo dinámico. Lo que funciona técnicamente también tiene que tener sentido en términos de gastos de capital, tarifas por hora de la máquina, esfuerzo de mantenimiento, costos de energía, compromiso de capital y depreciación. Enfoque únicamente en el ahorro de costos laborales o los tiempos de lejoración más cortos serían cortos visituosos”.
Teniendo en cuenta todos los factores técnicos, logísticos y financieros, existe una clara recomendación para implementar la solución de automatización recientemente desarrollada. Grobis está orgulloso de que su enfoque de simulación integrado también redujo el tiempo de planificación en aproximadamente un 25%. Pensar en la economía desde el principio ahorra bucles de revisión innecesarias durante la planificación.
Proporcionado por Fraunhofer Iwu
Cita: El nuevo concepto para materiales y la producción reduce drásticamente el tiempo de fabricación para las puertas de las aeronaves (2025, 29 de abril) recuperado el 29 de abril de 2025 de https://techxplore.com/news/2025-04-concept-materials-drasticalmente-aircraft.html
Este documento está sujeto a derechos de autor. Además de cualquier trato justo con el propósito de estudio o investigación privada, no se puede reproducir ninguna parte sin el permiso por escrito. El contenido se proporciona solo para fines de información.